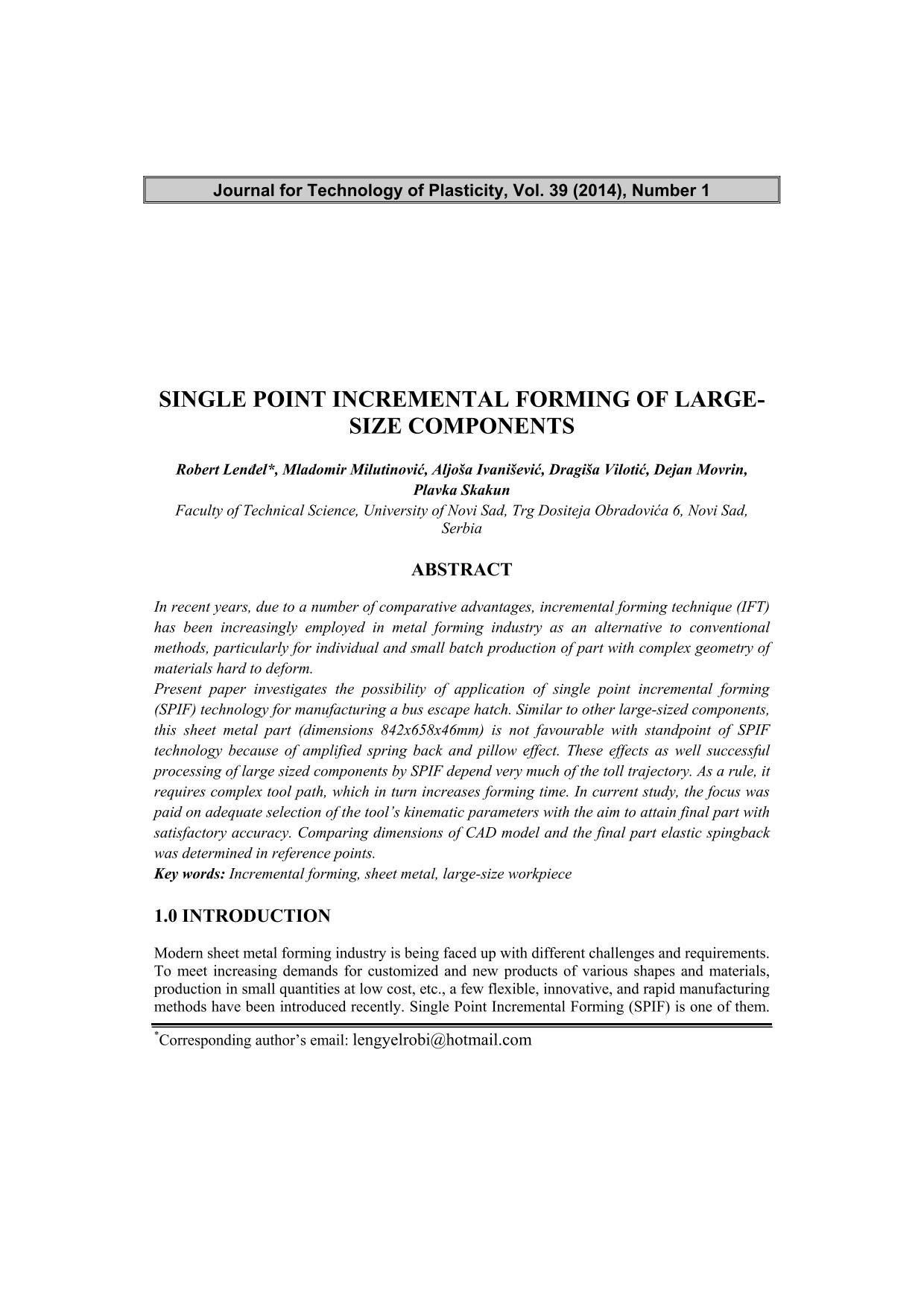
Published 2014-06-27
abstract views: 160 // Full text article (PDF): 0
Keywords
- Incremental forming,
- sheet metal,
- large-size workpiece
How to Cite

This work is licensed under a Creative Commons Attribution 4.0 International License.
Abstract
In recent years, due to a number of comparative advantages, incremental forming technique (IFT) has been increasingly employed in metal forming industry as an alternative to conventional methods, particularly for individual and small batch production of part with complex geometry of materials hard to deform.
Present paper investigates the possibility of application of single point incremental forming (SPIF) technology for manufacturing a bus escape hatch. Similar to other large-sized components, this sheet metal part (dimensions 842x658x46mm) is not favourable with standpoint of SPIF technology because of amplified spring back and pillow effect. These effects as well successful processing of large sized components by SPIF depend very much of the toll trajectory. As a rule, it requires complex tool path, which in turn increases forming time. In current study, the focus was paid on adequate selection of the tool’s kinematic parameters with the aim to attain final part with satisfactory accuracy. Comparing dimensions of CAD model and the final part elastic spingback was determined in reference points.