Comparative analysis of classical forging and orbital forging of cross joint component
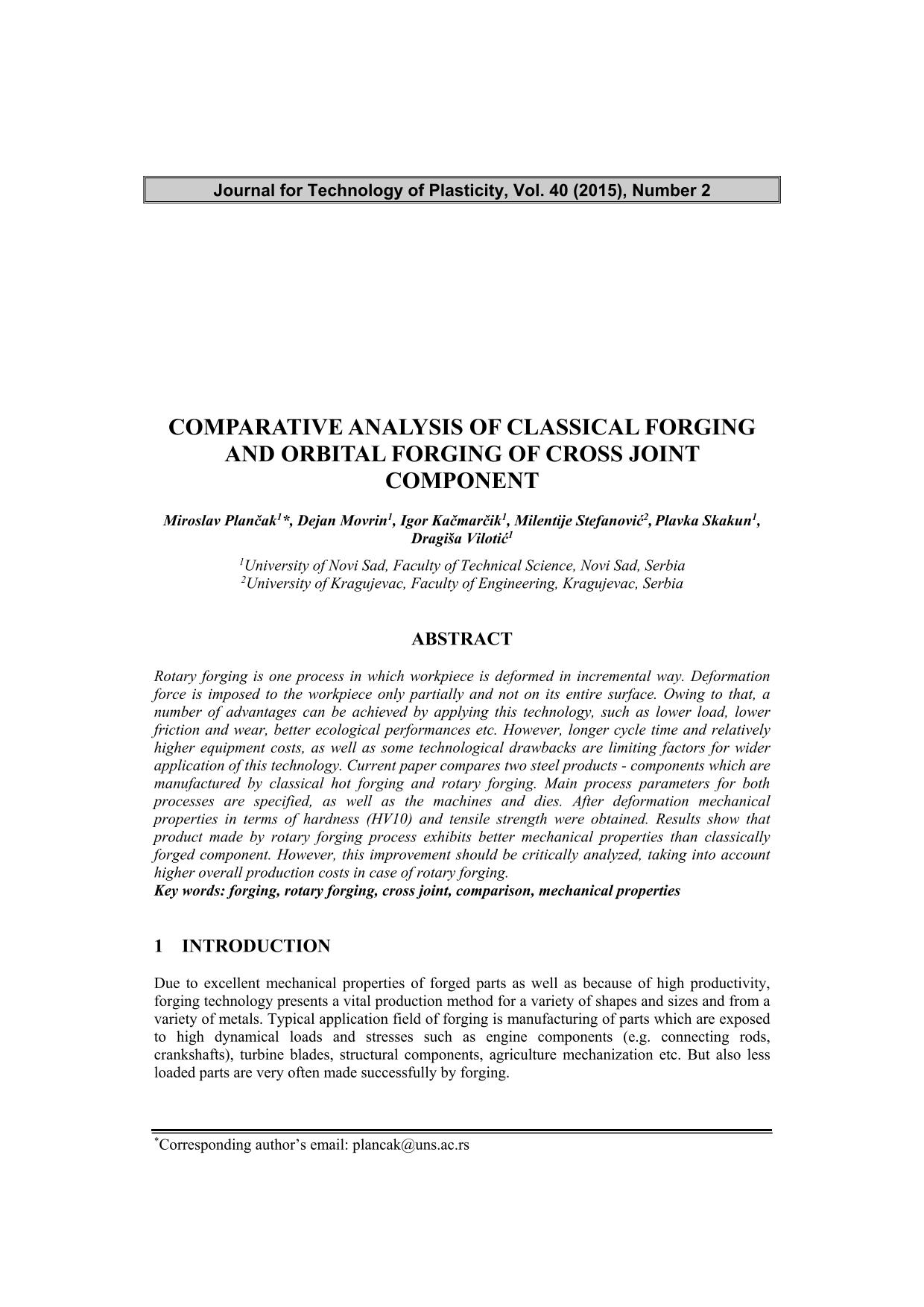
Published 2015-12-21
abstract views: 48 // Full text article (PDF): 0
Keywords
- forging,
- rotary forging,
- cross joint,
- comparison,
- mechanical properties
How to Cite

This work is licensed under a Creative Commons Attribution 4.0 International License.
Abstract
Rotary forging is one process in which workpiece is deformed in incremental way. Deformation force is imposed to the workpiece only partially and not on its entire surface. Owing to that, a number of advantages can be achieved by applying this technology, such as lower load, lower friction and wear, better ecological performances etc. However, longer cycle time and relatively higher equipment costs, as well as some technological drawbacks are limiting factors for wider application of this technology. Current paper compares two steel products - components which are manufactured by classical hot forging and rotary forging. Main process parameters for both processes are specified, as well as the machines and dies. After deformation mechanical properties in terms of hardness (HV10) and tensile strength were obtained. Results show that product made by rotary forging process exhibits better mechanical properties than classically forged component. However, this improvement should be critically analyzed, taking into account higher overall production costs in case of rotary forging.