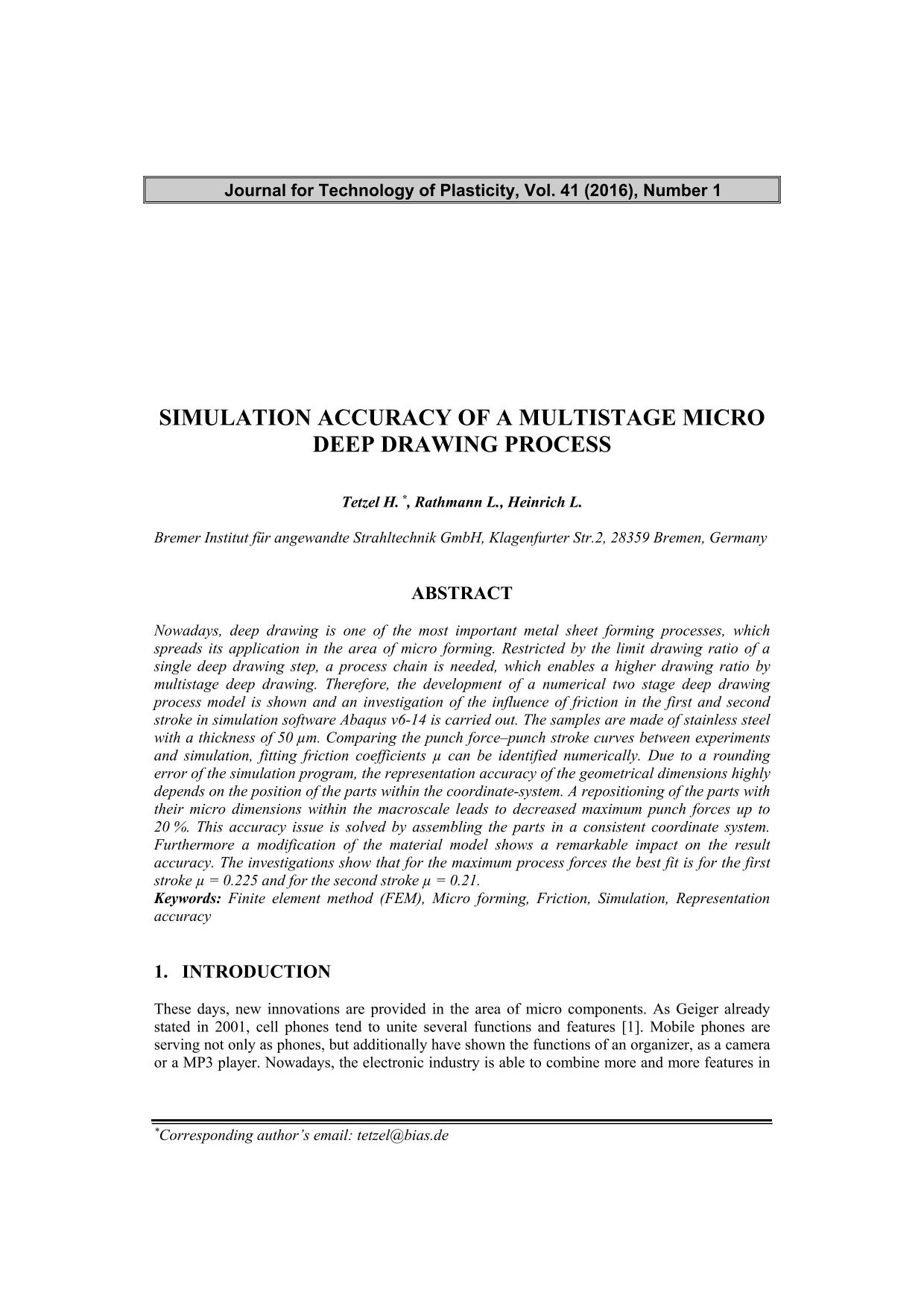
Published 2016-07-01
abstract views: 55 // Full text article (PDF): 0
Keywords
- Finite element method (FEM),
- Micro forming,
- Friction,
- Simulation,
- Representation accuracy
How to Cite

This work is licensed under a Creative Commons Attribution 4.0 International License.
Abstract
Nowadays, deep drawing is one of the most important metal sheet forming processes, which spreads its application in the area of micro forming. Restricted by the limit drawing ratio of a single deep drawing step, a process chain is needed, which enables a higher drawing ratio by multistage deep drawing. Therefore, the development of a numerical two stage deep drawing process model is shown and an investigation of the influence of friction in the first and second stroke in simulation software Abaqus v6-14 is carried out. The samples are made of stainless steel with a thickness of 50 µm. Comparing the punch force–punch stroke curves between experiments and simulation, fitting friction coefficients µ can be identified numerically. Due to a rounding error of the simulation program, the representation accuracy of the geometrical dimensions highly depends on the position of the parts within the coordinate-system. A repositioning of the parts with their micro dimensions within the macroscale leads to decreased maximum punch forces up to 20 %. This accuracy issue is solved by assembling the parts in a consistent coordinate system. Furthermore a modification of the material model shows a remarkable impact on the result accuracy. The investigations show that for the maximum process forces the best fit is for the first stroke µ = 0.225 and for the second stroke µ = 0.21.