Influence of prefom shape on die load and part accuracy in hot forging of pneumatic clamp
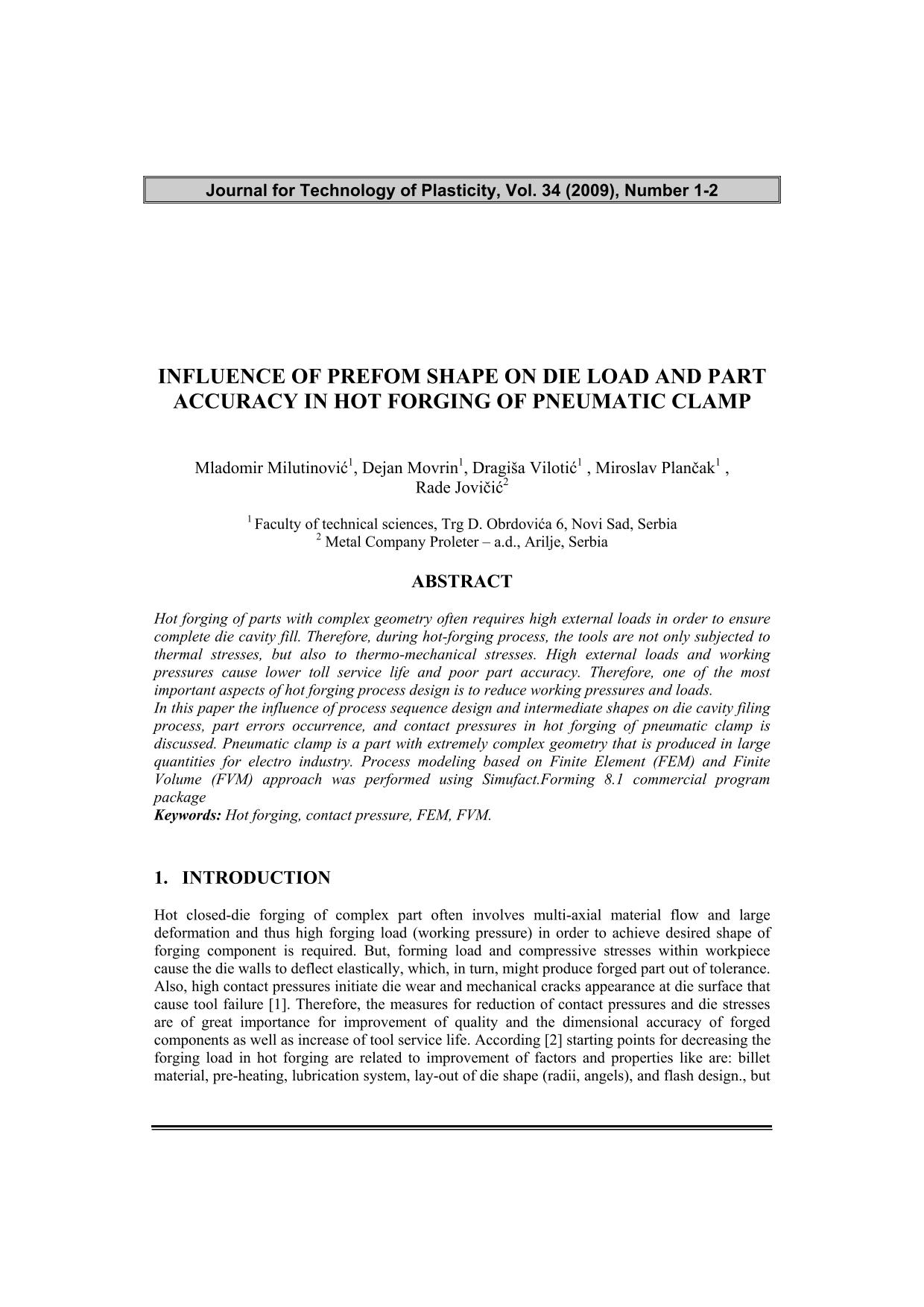
Published 2009-12-25
abstract views: 149 // Full text article (PDF): 43
Keywords
- Hot forging,
- contact pressure,
- FEM,
- FVM
How to Cite

This work is licensed under a Creative Commons Attribution 4.0 International License.
Abstract
Hot forging of parts with complex geometry often requires high external loads in order to ensure complete die cavity fill. Therefore, during hot-forging process, the tools are not only subjected to thermal stresses, but also to thermo-mechanical stresses. High external loads and working pressures cause lower toll service life and poor part accuracy. Therefore, one of the most important aspects of hot forging process design is to reduce working pressures and loads. In this paper the influence of process sequence design and intermediate shapes on die cavity filing process, part errors occurrence, and contact pressures in hot forging of pneumatic clamp is discussed. Pneumatic clamp is a part with extremely complex geometry that is produced in large quantities for electro industry. Process modeling based on Finite Element (FEM) and Finite Volume (FVM) approach was performed using Simufact.Forming 8.1 commercial program package.