Impact of stress exponent on creep behavior in a rotating composite disc with hyperbolic thickness
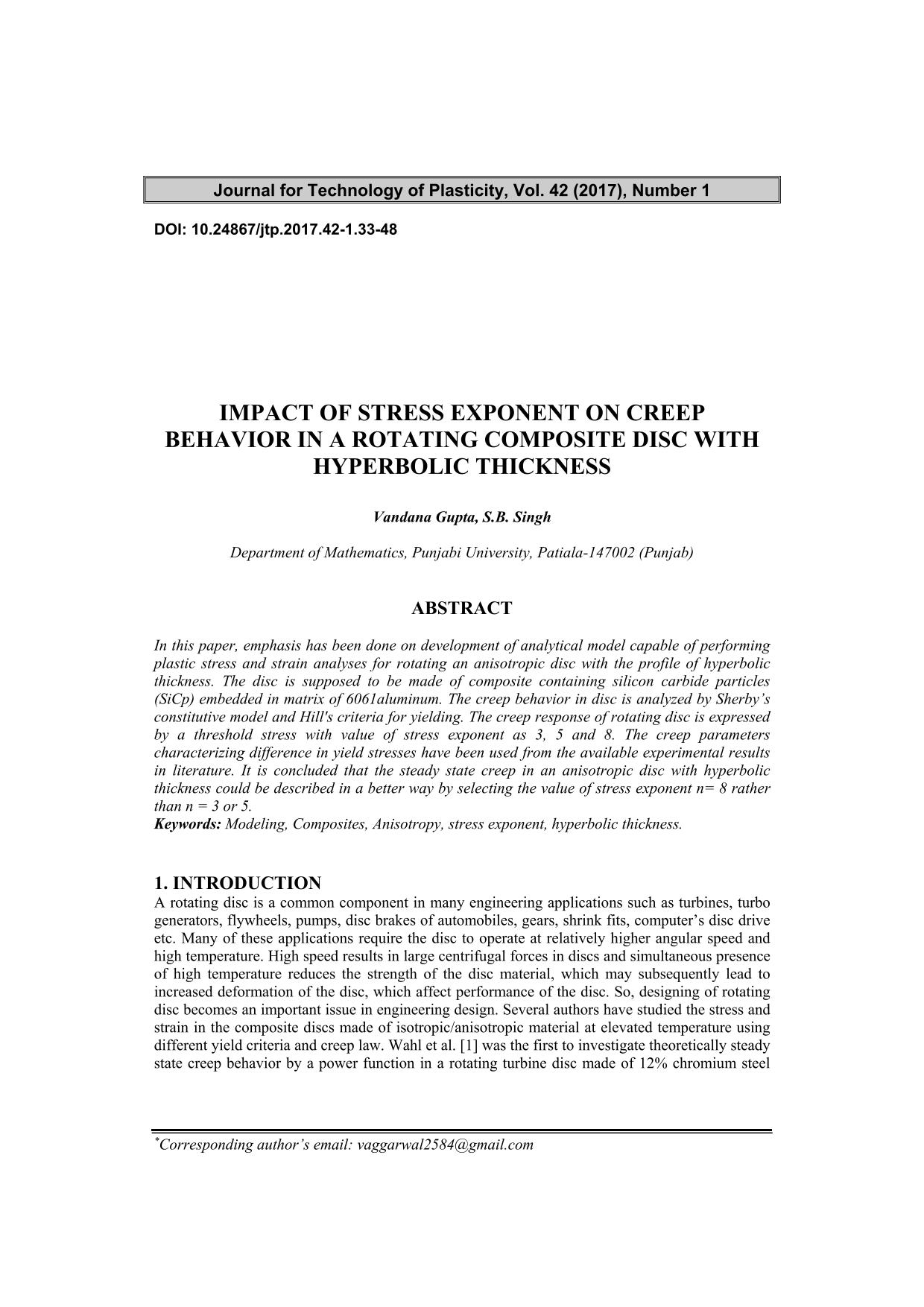
Published 2017-06-30
abstract views: 139 // Full text article (PDF): 0
Keywords
- Modeling,
- Composites,
- Anisotropy,
- stress exponent,
- hyperbolic thickness
How to Cite

This work is licensed under a Creative Commons Attribution 4.0 International License.
Abstract
In this paper, emphasis has been done on development of analytical model capable of performing plastic stress and strain analyses for rotating an anisotropic disc with the profile of hyperbolic thickness. The disc is supposed to be made of composite containing silicon carbide particles (SiCp) embedded in matrix of 6061aluminum. The creep behavior in disc is analyzed by Sherby’s constitutive model and Hill's criteria for yielding. The creep response of rotating disc is expressed by a threshold stress with value of stress exponent as 3, 5 and 8. The creep parameters characterizing difference in yield stresses have been used from the available experimental results in literature. It is concluded that the steady state creep in an anisotropic disc with hyperbolic thickness could be described in a better way by selecting the value of stress exponent n= 8 rather than n = 3 or 5.