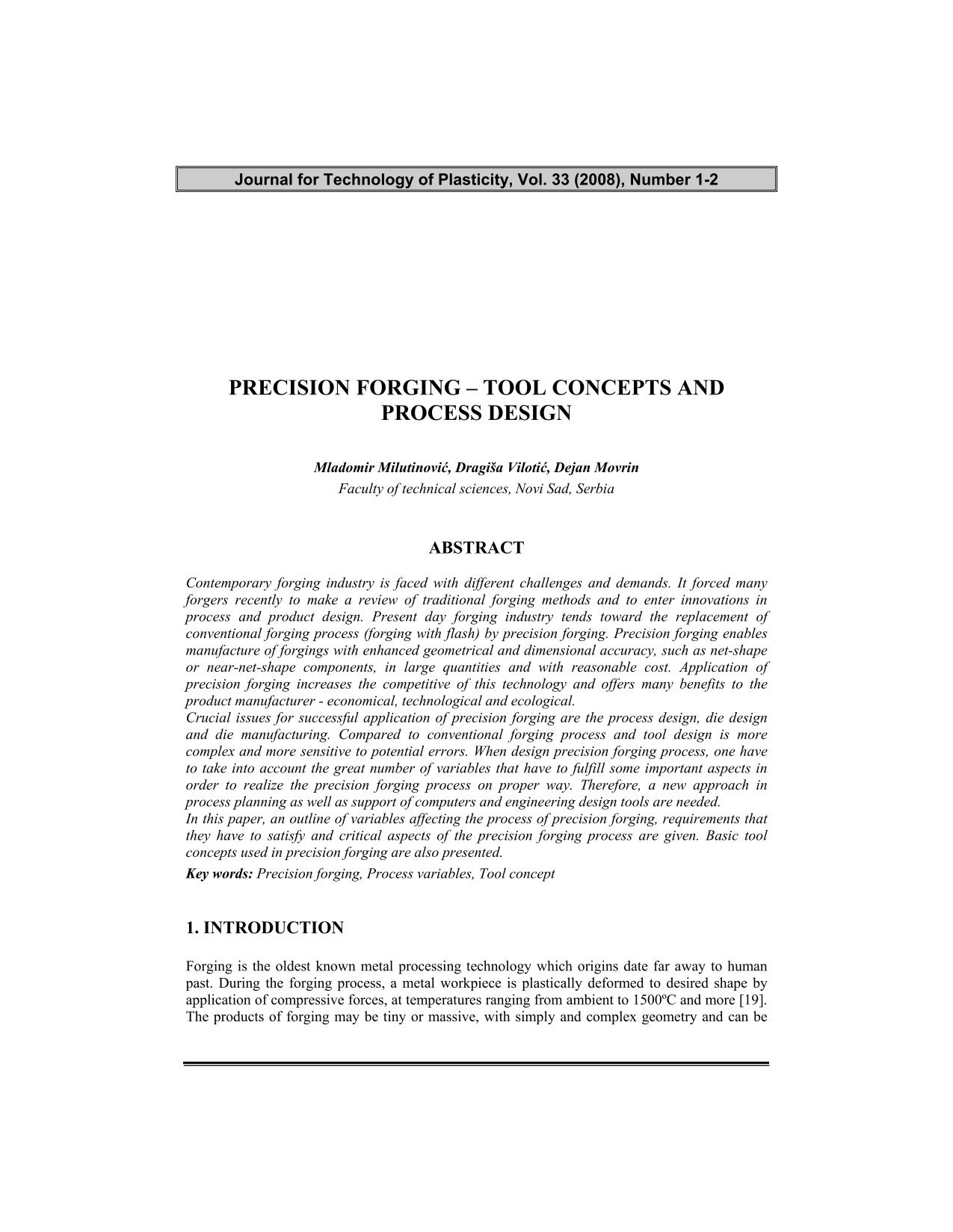
Published 2008-12-26
abstract views: 149 // Full text article (PDF): 94
Keywords
- Precision forging,
- Process variables,
- Tool concept
How to Cite

This work is licensed under a Creative Commons Attribution 4.0 International License.
Abstract
Contemporary forging industry is faced with different challenges and demands. It forced many forgers recently to make a review of traditional forging methods and to enter innovations in process and product design. Present day forging industry tends toward the replacement of conventional forging process (forging with flash) by precision forging. Precision forging enables manufacture of forgings with enhanced geometrical and dimensional accuracy, such as net-shape or near-net-shape components, in large quantities and with reasonable cost. Application of precision forging increases the competitive of this technology and offers many benefits to the product manufacturer - economical, technological and ecological. Crucial issues for successful application of precision forging are the process design, die design and die manufacturing. Compared to conventional forging process and tool design is more complex and more sensitive to potential errors. When design precision forging process, one have to take into account the great number of variables that have to fulfill some important aspects in order to realize the precision forging process on proper way. Therefore, a new approach in process planning as well as support of computers and engineering design tools are needed. In this paper, an outline of variables affecting the process of precision forging, requirements that they have to satisfy and critical aspects of the precision forging process are given. Basic tool concepts used in precision forging are also presented.