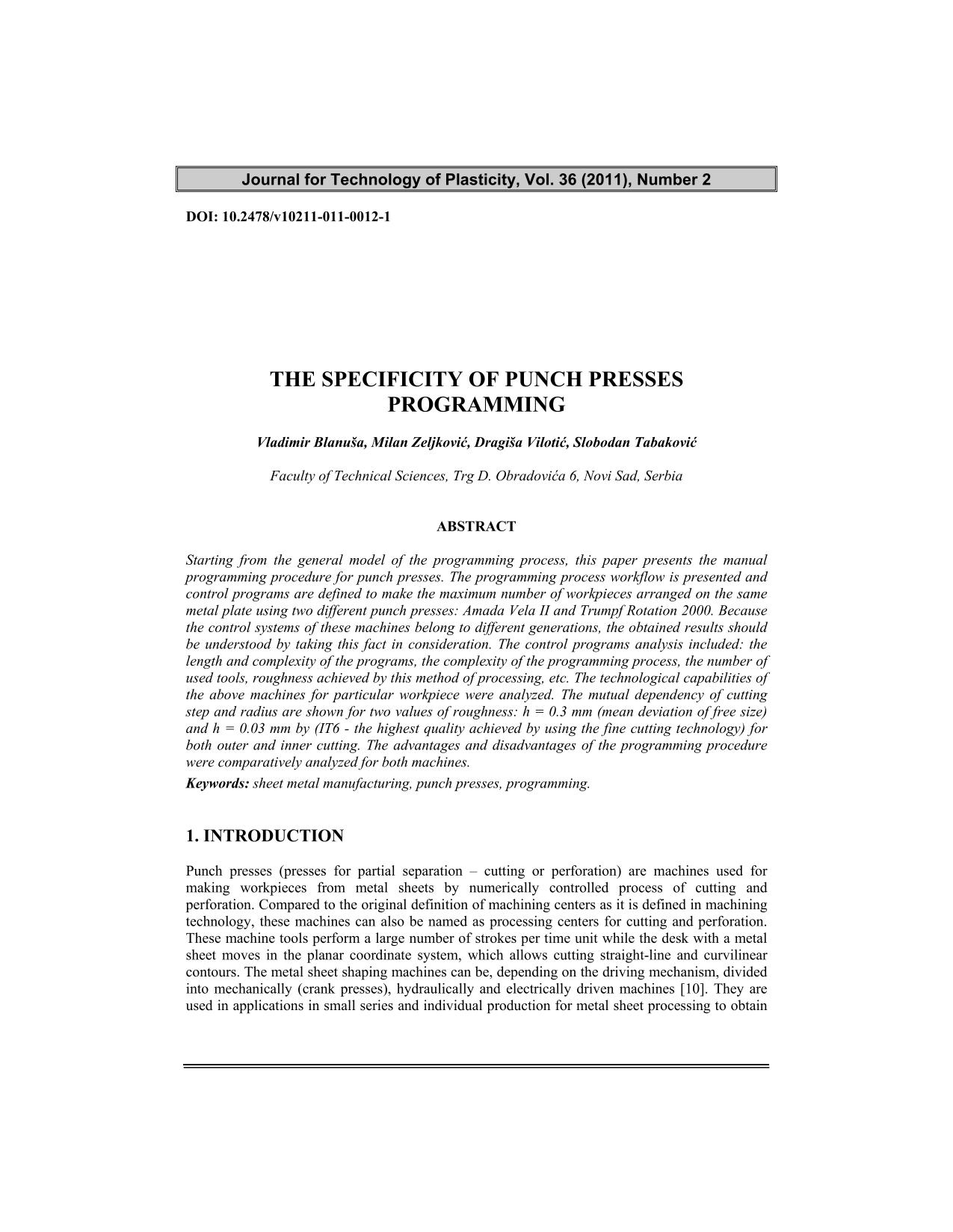
Published 2011-12-30
abstract views: 33 // Full text article (PDF): 6
Keywords
- sheet metal manufacturing,
- punch presses,
- programming
How to Cite
Copyright (c) 2011 This work is licensed under a Creative Commons Attribution 4.0 International License.

This work is licensed under a Creative Commons Attribution 4.0 International License.
Abstract
Starting from the general model of the programming process, this paper presents the manual programming procedure for punch presses. The programming process workflow is presented and control programs are defined to make the maximum number of workpieces arranged on the same metal plate using two different punch presses: Amada Vela II and Trumpf Rotation 2000. Because the control systems of these machines belong to different generations, the obtained results should be understood by taking this fact in consideration. The control programs analysis included: the length and complexity of the programs, the complexity of the programming process, the number of used tools, roughness achieved by this method of processing, etc. The technological capabilities of the above machines for particular workpiece were analyzed. The mutual dependency of cutting step and radius are shown for two values of roughness: h = 0.3 mm (mean deviation of free size) and h = 0.03 mm by (IT6 - the highest quality achieved by using the fine cutting technology) for both outer and inner cutting. The advantages and disadvantages of the programming procedure were comparatively analyzed for both machines.