Study of quality indicators of gravure imprints obtained with fluorescent ink
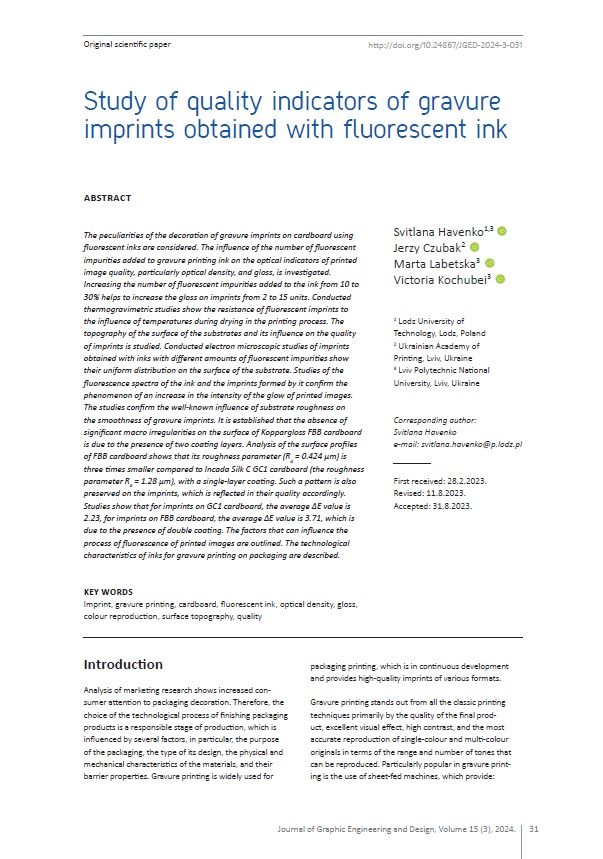
Published 2024-09-01
abstract views: 270 // Full text article (PDF): 212
Keywords
- Imprint,
- gravure printing,
- cardboard,
- fluorescent ink,
- optical density
- gloss,
- colour reproduction,
- surface topography,
- quality ...More
How to Cite
Abstract
The peculiarities of the decoration of gravure imprints on cardboard using fluorescent inks are considered. The influence of the number of fluorescent impurities added to gravure printing ink on the optical indicators of printed image quality, particularly optical density, and gloss, is investigated. Increasing the number of fluorescent impurities added to the ink from 10 to 30% helps to increase the gloss on imprints from 2 to 15 units. Conducted thermogravimetric studies show the resistance of fluorescent imprints to the influence of temperatures during drying in the printing process. The topography of the surface of the substrates and its influence on the quality of imprints is studied. Conducted electron microscopic studies of imprints obtained with inks with different amounts of fluorescent impurities show their uniform distribution on the surface of the substrate. Studies of the fluorescence spectra of the ink and the imprints formed by it confirm the phenomenon of an increase in the intensity of the glow of printed images. The studies confirm the well-known influence of substrate roughness on the smoothness of gravure imprints. It is established that the absence of significant macro irregularities on the surface of Koppargloss FBB cardboard is due to the presence of two coating layers. Analysis of the surface profiles of FBB cardboard shows that its roughness parameter (Ra = 0.424 μm) is three times smaller compared to Incada Silk С GC1 cardboard (the roughness parameter Ra = 1.28 μm), with a single-layer coating. Such a pattern is also preserved on the imprints, which is reflected in their quality accordingly. Studies show that for imprints on GC1 cardboard, the average ΔE value is 2.23, for imprints on FBB cardboard, the average ΔE value is 3.71, which is due to the presence of double coating. The factors that can influence the process of fluorescence of printed images are outlined. The technological characteristics of inks for gravure printing on packaging are described.
Article history: Received (Februar 28, 2023); Revised (August 11, 2023); Accepted (August 31, 2023); Published online (September 1, 2024)
Dimensions Citation Metrics
References
- Bohan, M. F. J., Claypole, T. C. & Gethin, D. T. (2000) The effect of process parameters on product quality of rotogravure printing. Proceedings of the Institution of Mechanical Engineers, Part B: Journal of Engineering Manufacture. 214 (3), 205-219. Available from: doi: 10.1243/0954405001517595
- Ceyhan, U. (2016) Fluid Mechanics Problems Motivated by Gravure Printing of Electronics. PhD thesis. University of California, Berkeley.
- Edinburgh Instruments (2023) FS5 Spectrofluorometer. Available from: https://www.edinst.com/us/products/fs5-spectrofluorometer/
- Elastoform. (2023) Luminophore redred-orange glow. Up. 10 g. Glow-in-the-dark pigment. Available from: https://elastoform.com.ua/ua/p727490382-lyuminofor-krasnyjkrasno-oranzhevoe.html
- El-Sherbiny, S. (2003) The influence of some paper parameters on gravure print quality. Surface Coatings International Part B: Coatings Transactions. 86 (4), 263-271. Available from: doi: 10.1007/BF02699498
- Goyat, A., Singh, N. & Sharma, S. (2018) Investigation of web-fed gravure printing for optimization of job change over time. International Journal of Engineering Sciences & Research Technology. 7 (1), 192-195. Available from: doi: 10.5281/zenodo.1135964
- Gravure Association of America. & Gravure Education Foundation. (1991) Gravure: process and technology. Rochester, Gravure Association of America, Gravure Education Foundation.
- Holmen. (2023) Paperboard know-how, general technical information. Available from: https://www.iggesund.com/insights/paperboard-know-how/general-technical-information/#accordion-step-by-step-20006
- International Organization for Standardization. (2007) ISO 12647-4:2007. Graphic technology - Process control for the production of half-tone colour separations, proofs and production prints — Part 4: Publication gravure printing. Geneva, International Organization for Standardization.
- Menczel, J. D. & Prime, B. R. (2008) Thermal Analysis of Polymers: Fundamentals and Applications. Hoboken, John Wiley & Sons, Inc.
- Pilc, W. (2007) Characterization of gravure printing techniques. Radom Institute for Sustainable Technologies. National Research Institute. 4.
- Szentgyörgyvölgyi, R. (2016) Gravure Printing. In: Izdebska, J. & Thomas, S. (eds.) Printing on Polymers - Fundamentals and Applications. Amsterdam, Netherlands, Elsevier, pp. 199 - 215. Available from: doi: 10.1016/B978-0-323-37468-2.00012-9
- Wessendorf, A. (2012) Gravure package printing under pressure. Flexo Gravure Global. 18 (4-2012), 50-54.
- Wu, Y. J. (2008) The Effect of Substrate Properties on Print Attributes for Gravure Printing - From Proof to Press. PhD thesis. Western Michigan University.