Changes in the surface roughness of aluminium oxide (non-printing) areas on offset printing plate depending on number of imprints
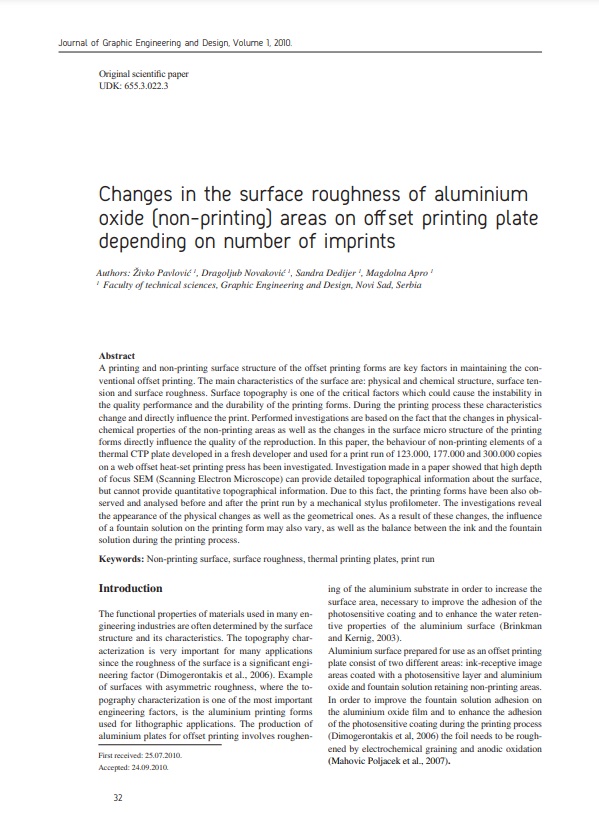
Published 2023-10-01
abstract views: 153 // Full text article (PDF): 126
Keywords
- Non-printing surface,
- surface roughness,
- thermal printing plates,
- print run
How to Cite
Copyright (c) 2010 © 2010 Authors. Published by the University of Novi Sad, Faculty of Technical Sciences, Department of Graphic Engineering and Design. This article is an open access article distributed under the terms and conditions of the Creative Commons Attribution license 3.0 Serbia.

This work is licensed under a Creative Commons Attribution 3.0 Unported License.
Abstract
-
A printing and non-printing surface structure of the offset printing forms are key factors in maintaining the conventional offset printing. The main characteristics of the surface are: physical and chemical structure, surface tension and surface roughness. Surface topography is one of the critical factors which could cause the instability in the quality performance and the durability of the printing forms. During the printing process these characteristics change and directly influence the print. Performed investigations are based on the fact that the changes in physicalchemical properties of the non-printing areas as well as the changes in the surface micro structure of the printing forms directly influence the quality of the reproduction. In this paper, the behaviour of non-printing elements of a thermal CTP plate developed in a fresh developer and used for a print run of 123.000, 177.000 and 300.000 copies on a web offset heat-set printing press has been investigated. Investigation made in a paper showed that high depth of focus SEM (Scanning Electron Microscope) can provide detailed topographical information about the surface, but cannot provide quantitative topographical information. Due to this fact, the printing forms have been also observed and analysed before and after the print run by a mechanical stylus profilometer. The investigations reveal the appearance of the physical changes as well as the geometrical ones. As a result of these changes, the influence of a fountain solution on the printing form may also vary, as well as the balance between the ink and the fountain solution during the printing process.